Packaging is a critical aspect of the cement manufacturing process. The right type of packaging ensures that the cement reaches its destination in good condition, maintains its quality, and remains easy to handle and store. In recent years, cement manufacturers have been increasingly shifting to block bottom bags for packaging their products. These bags are becoming the preferred choice over traditional packaging options such as open-mouth bags or paper sacks, thanks to their superior durability, functionality, and efficiency.
This blog explores why cement manufacturers are making the switch to block bottom bags for packaging and how these bags offer significant advantages for the cement industry.
Understanding Block Bottom Bags
Before diving into why cement manufacturers are opting for block bottom bags, it’s essential to understand what makes these bags unique. Block bottom bags are made from strong paper materials, typically multi-ply kraft paper, which is laminated to ensure strength and durability. These bags are designed with a flat, square base that allows them to stand upright, making them easy to fill, store, and stack.
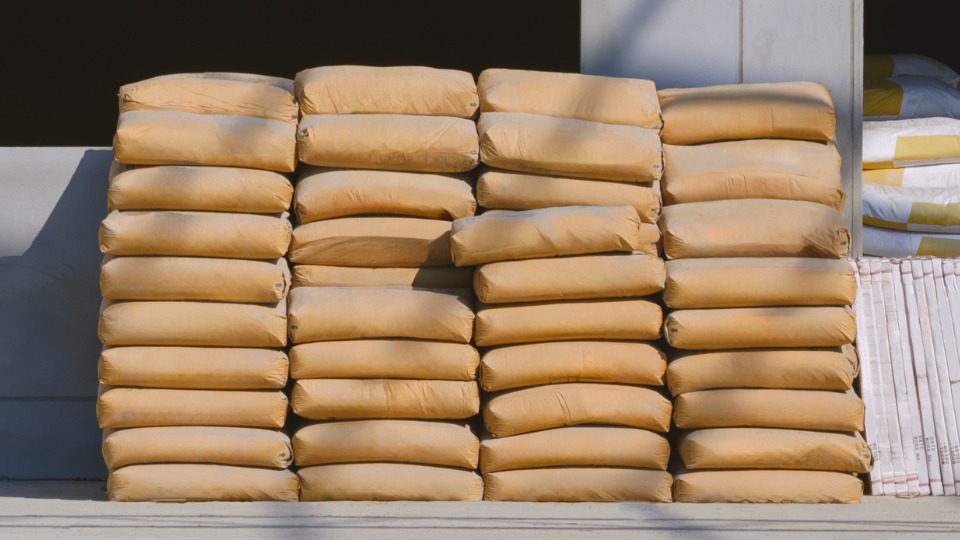
Unlike traditional bags that may be flimsy or unstable, the block bottom design provides excellent support and stability. These bags are commonly used in packaging heavy materials such as cement, chemicals, and flour because of their ability to hold weight and maintain their shape.
Key Benefits of Block Bottom Bags for Cement Packaging
Cement packaging requires durability, stability, and safety. Block bottom bags offer several advantages that make them the ideal choice for cement manufacturers. Below are some of the most compelling reasons why cement manufacturers are switching to block bottom bags.
1. Enhanced Durability and Strength
One of the primary reasons manufacturers are switching to block bottom bags is their superior durability. Cement, being a heavy and fine material, needs packaging that can withstand rough handling during transportation and storage. Traditional packaging, such as open-mouth bags or woven sacks, can tear or break under pressure, resulting in product loss and additional costs.
Block bottom bags, on the other hand, are made from multiple layers of kraft paper and often reinforced with additional materials, making them highly resistant to tearing and puncturing. This strength ensures that the bags can handle the weight and abrasiveness of cement without compromising the integrity of the packaging.
2. Increased Efficiency in Filling and Storing
The block bottom design provides a flat, stable base that allows the bags to stand upright, making them easier to fill and store. This is especially important in cement packaging, where speed and accuracy are crucial. The stability of block bottom bags allows for quick and efficient filling, reducing labor costs and minimizing the risk of spillage or waste.
Additionally, because these bags stand upright, they are easier to stack, which maximizes storage space in warehouses and on transport vehicles. This efficient use of space helps cement manufacturers optimize their supply chain, reducing transportation costs and improving overall operational efficiency.
3. Better Protection of Cement Quality
Cement is a product that is highly susceptible to environmental factors such as moisture, humidity, and contamination. Traditional packaging options may not provide the level of protection needed to preserve the quality of the cement, especially when exposed to harsh conditions during transportation or storage.
Block bottom bags are designed to provide a more secure seal and protect the contents from external elements. These bags are often laminated to prevent moisture from seeping in, ensuring that the cement remains dry and of high quality. The reinforced structure of the block bottom bag also provides protection against physical damage, keeping the cement intact and free from contamination.
4. Sustainability and Eco-Friendliness
In recent years, there has been increasing pressure on manufacturers to adopt more sustainable practices and reduce their environmental footprint. The cement industry, being energy-intensive, is especially focused on minimizing its environmental impact. Block bottom bags offer a more eco-friendly alternative to traditional packaging options.
These bags are typically made from recyclable kraft paper, making them easier to dispose of without contributing to landfill waste. Additionally, the durability of block bottom bags means that fewer bags are needed to package the same amount of cement, reducing the overall amount of packaging waste.
Many cement manufacturers are also opting for biodegradable coatings for their block bottom bags, further improving their sustainability credentials. By switching to block bottom bags, cement manufacturers can reduce their environmental impact while still providing effective, high-quality packaging for their products.
5. Improved Branding and Consumer Perception
In today’s competitive market, branding plays an important role in differentiating products. Cement packaging is no exception, and manufacturers are increasingly using packaging to reinforce their brand image and communicate their commitment to quality.
Block bottom bags offer a high-quality appearance and can be easily customized with logos, colors, and product information. The bags’ clean and professional design not only enhances the product’s shelf appeal but also conveys a sense of reliability and professionalism, which can improve consumer perception of the brand.
Additionally, the durability and functional design of block bottom bags send a message to consumers that the manufacturer cares about the quality and safety of the product. This can build trust and strengthen the brand’s reputation in the market.
6. Cost-Effectiveness in the Long Run
While block bottom bags may have a slightly higher initial cost compared to traditional packaging options, they offer significant long-term savings. The durability of these bags reduces the risk of product loss due to tears or damage, leading to fewer complaints and returns. The enhanced efficiency in filling, storing, and transporting cement also translates to reduced labor and shipping costs, further improving the overall profitability of the business.
Moreover, the use of block bottom bags may lead to greater customer satisfaction, as the bags’ robust design helps prevent spills and ensures that customers receive their products in the best possible condition. Happy customers are more likely to return, increasing repeat business and generating positive word-of-mouth recommendations.
7. Compliance with Regulatory Standards
Cement packaging is subject to various regulatory requirements, especially in terms of safety and labeling. Block bottom bags can easily accommodate the necessary regulatory markings and labels, ensuring that manufacturers remain in compliance with local laws and international standards. The ability to include clear, legible product information on the bags also ensures that customers and distributors can easily access important details such as weight, usage instructions, and handling precautions.
Conclusion
As the cement industry continues to evolve, manufacturers are increasingly recognizing the benefits of switching to block bottom bags for packaging. These bags offer enhanced durability, greater efficiency, and improved protection of cement quality, while also providing a more sustainable, cost-effective solution.
The superior strength of block bottom bags ensures that cement products remain safe and intact during transportation and storage, while the eco-friendly materials and sustainable design meet the growing demand for environmentally responsible packaging.
With the ability to boost branding, reduce costs, and improve overall operational efficiency, it’s no wonder that cement manufacturers are making the shift to block bottom bags. By investing in this innovative packaging solution, manufacturers can not only improve their business operations but also align with modern consumer preferences and environmental standards.
As the cement industry continues to grow, embracing block bottom bags is an important step in the direction of both quality and sustainability.